7 Easy Facts About Alcast Company Shown
7 Easy Facts About Alcast Company Shown
Blog Article
The Ultimate Guide To Alcast Company
Table of ContentsThe Definitive Guide to Alcast CompanyAlcast Company - QuestionsAbout Alcast CompanySome Known Details About Alcast Company Indicators on Alcast Company You Should KnowHow Alcast Company can Save You Time, Stress, and Money.
Chemical Contrast of Cast Aluminum Alloys Silicon promotes castability by minimizing the alloy's melting temperature and improving fluidity throughout casting. Furthermore, silicon contributes to the alloy's strength and wear resistance, making it useful in applications where durability is important, such as automobile parts and engine parts.It likewise improves the machinability of the alloy, making it simpler to refine into completed products. In this method, iron contributes to the general workability of light weight aluminum alloys.
Manganese contributes to the stamina of aluminum alloys and boosts workability (aluminum casting company). It is generally made use of in functioned aluminum products like sheets, extrusions, and accounts. The visibility of manganese help in the alloy's formability and resistance to fracturing during fabrication processes. Magnesium is a light-weight component that gives stamina and effect resistance to light weight aluminum alloys.
Rumored Buzz on Alcast Company
Zinc improves the castability of aluminum alloys and assists regulate the solidification procedure during casting. It boosts the alloy's strength and hardness.
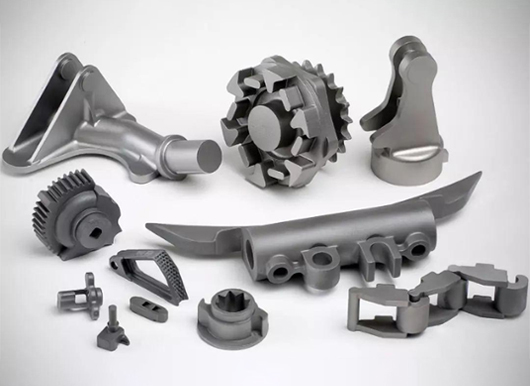
The main thermal conductivity, tensile strength, return strength, and prolongation vary. Select ideal basic materials according to the efficiency of the target product generated. Among the above alloys, A356 has the highest possible thermal conductivity, and A380 and ADC12 have the most affordable. The tensile limitation is the contrary. A360 has the very best yield toughness and the highest prolongation price.
About Alcast Company

In precision spreading, 6063 is appropriate for applications where complex geometries and high-grade surface coatings are extremely important. Examples consist of telecommunication enclosures, where the alloy's superior formability permits streamlined and visually pleasing layouts while keeping architectural integrity. In a similar way, in the Lighting Solutions sector, precision-cast 6063 elements produce classy and efficient illumination fixtures read here that call for detailed forms and good thermal performance.
It results in a finer surface coating and far better deterioration resistance in A360. In addition, the A360 exhibits remarkable prolongation, making it ideal for facility and thin-walled components. In precision spreading applications, A360 is appropriate for markets such as Customer Electronics, Telecommunication, and Power Devices. Its improved fluidity enables elaborate, high-precision components like smartphone casings and communication gadget real estates.
How Alcast Company can Save You Time, Stress, and Money.
Its distinct properties make A360 a beneficial choice for accuracy spreading in these industries, boosting item resilience and top quality. aluminum metal casting. Light weight aluminum alloy 380, or A380, is a commonly used spreading alloy with several distinct features.
In precision spreading, aluminum 413 beams in the Consumer Electronic Devices and Power Equipment industries. This alloy's premium deterioration resistance makes it a superb choice for outdoor applications, making certain lasting, durable items in the mentioned industries.
The Alcast Company Diaries
The light weight aluminum alloy you choose will considerably influence both the casting process and the properties of the last item. Since of this, you must make your choice meticulously and take an informed approach.
Identifying the most suitable aluminum alloy for your application will certainly imply evaluating a vast variety of qualities. The initial group addresses alloy qualities that influence the manufacturing process.
Some Known Questions About Alcast Company.
The alloy you pick for die spreading straight influences several aspects of the casting process, like how easy the alloy is to function with and if it is prone to casting flaws. Warm cracking, also referred to as solidification splitting, is a common die casting defect for aluminum alloys that can lead to interior or surface-level tears or cracks.
Specific light weight aluminum alloys are much more prone to warm breaking than others, and your option must consider this. It can harm both the actors and the die, so you ought to look for alloys with high anti-soldering properties.
Corrosion resistance, which is already a significant feature of light weight aluminum, can differ considerably from alloy to alloy and is an important characteristic to take into consideration depending upon the environmental problems your product will certainly be revealed to (aluminum foundry). Use resistance is an additional property frequently looked for in light weight aluminum items and can distinguish some alloys
Report this page